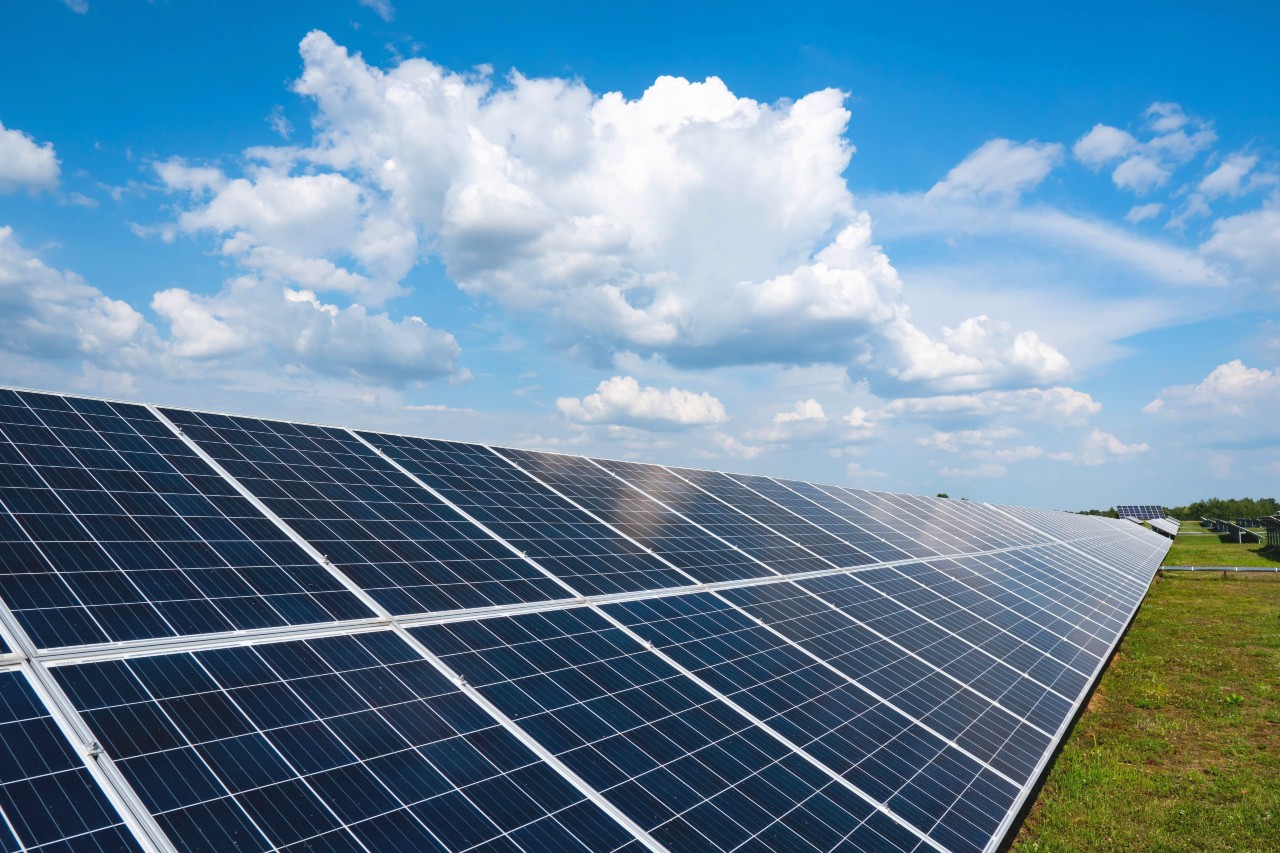
Energy audit case study – progressive winery goes even further
Energy efficiency has been a hot topic lately, for both industries and governments. This has been driven by rising power prices, grid instabilities and the advances in solar and storage technologies that allow businesses to take more control of their energy supply. Several state governments have established grant schemes for businesses to conduct energy audits and perform upgrades that reduce energy use. Sustainability Victoria’s Energy Assessment Grants scheme, which is available to wineries in Victoria, is accepting applications until September 2018. Agriculture Victoria has also recently launched its Agriculture Energy Investment Plan which provides on-farm energy assessments for grapegrowers in Victoria. The AWRI website (https://www.awri.com.au/information_services/grants/) provides a list of grants available to grapegrowers and wineries; however, even without a grant, an energy audit can still be a valuable exercise.
Affinity Labs recently performed an energy audit for a medium-sized winery (3,500 t crush) in north-east Victoria. This winery had already taken a number of steps to improve its energy efficiency, but wanted assistance to identify some of the less obvious opportunities for improvement. Benchmarking against other wineries of similar size in the membership database of Entwine (Australia’s wine sector sustainability program) showed that the winery was already in the top 15% of performance in terms of electricity use per tonne of grapes crushed. This had been achieved through:
- installation of a 100 kW solar photovoltaic system which covered approximately a quarter of the winery’s electricity use, with 70% of electricity generated used on-site and 30% exported to the grid
- installation of LED lighting inside the cellar and throughout the outdoor tank farm, which reduced electricity use on lighting by 66%
- replacement of an old chiller with two modern packaged chillers, which allowed one to be run year-round and the second to be only used during vintage when required. Heat recovery was also installed on the primary chiller to pre-heat water for the boiler
- switching from rotary drum vacuum filtration to cross-flow filtration.
Between 2004 and 2017, the winery reduced its expenditure on grid electricity by almost 60% even though electricity prices increased over that time. An energy audit was requested to investigate the potential to find even more efficiencies.
Case study
The audit started by investigating the winery’s energy trends, equipment usage and winemaking regime to estimate the breakdown of electricity use throughout the winery. This is shown in Figure 1. Breakdown of winery electricity use identified during the energy audit, with a further breakdown of the electricity used for refrigeration.
Refrigeration accounted for 34% of site electricity use, which is less than the 50–70% often seen in large wineries (AWRI 2012). But the most striking aspect was the electricity used by the aerator on the winery’s wastewater dam. The winery had an unmanaged aerobic wastewater treatment dam that ran continuously through vintage and then eight hours per day outside that period. This appeared to be excessive. On closer inspection, two factors were found to be contributing to this. The pH management of the dam was not ideal, so the bacteria present were not performing as efficiently as they could. There was also no dissolved oxygen (DO) measurement on the dam, so the aerator may have been running more than needed. Based on recommendations following the audit, the winery has now installed a DO meter in order to run the aerator based on a DO set point instead of a timer. Recent performance (outside of vintage) with the new meter has seen the aerator only running 10% of the time, rather than the eight hours per day it was running based on the timer.
The air compressor at the site only ran for approximately 800 hours per year and its principal role was to service the membrane presses during vintage. Despite this limited use it still was responsible for 9% of the annual site electricity consumption. The compressed air system had never been audited so further investigation was recommended to evaluate its performance and check the system for leaks. Small leaks in compressed gas systems can lead to large energy losses. It has been estimated by the US Department of Energy (2004) that typical losses from compressed air systems can be around 20–30%, whereas well-maintained systems lose less than 10%.
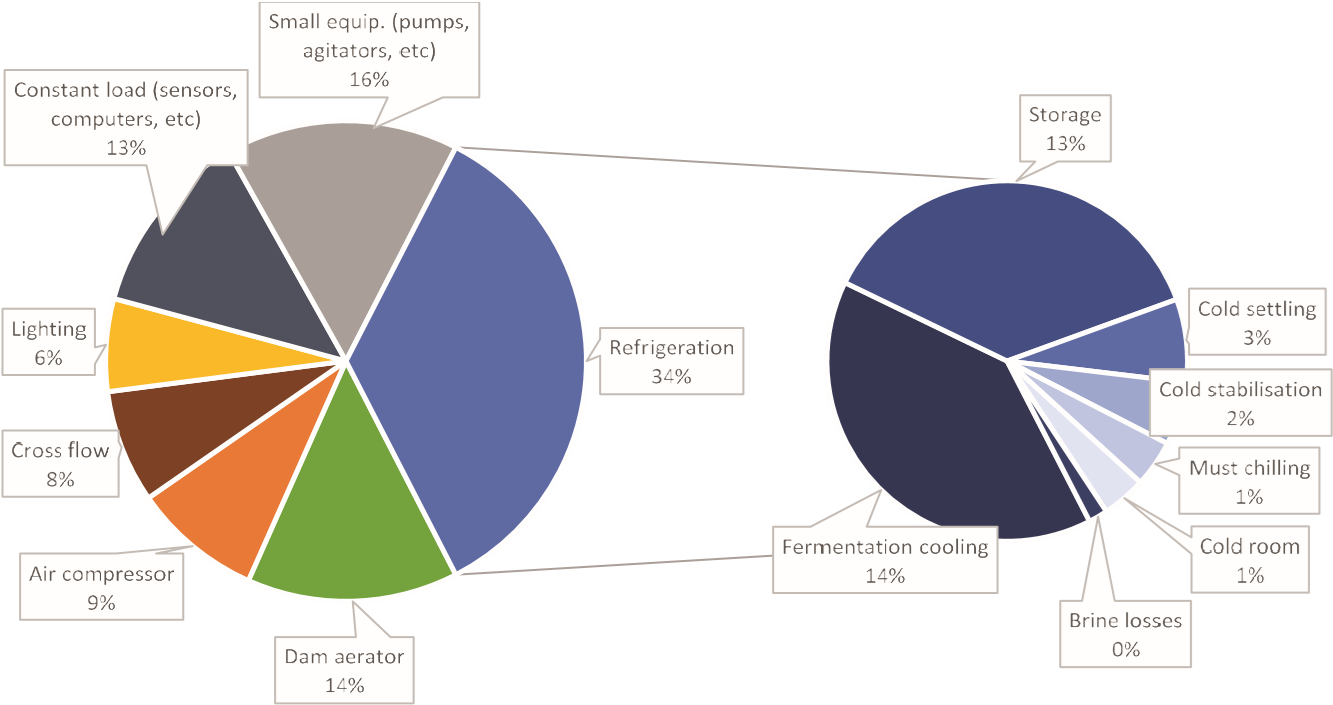
As previously mentioned, refrigeration use at the winery was lower than industry averages, but an opportunity was identified for further savings to be realised through modifying wine storage temperatures. White wines, which made up the majority of the winery’s production, were stored at 2°C, which is excessively cool. The rationale for this was to preserve wine freshness, but a recommendation was made to raise this to 7°C (5–10°C is typical in Australia). Importantly, this would also allow the winery to run warmer brine when cold settling and cold stabilisation were not being performed. The winery generally runs -5°C brine all year round, but if the lowest temperature required in the winery is 7°C, then it could feasibly run with 2°C brine for about six months of the year. This would provide an increase in efficiency of 15%, based on the technical specifications of its chillers.
The winery preferred flotation over cold settling in principle, not only to save energy but also as a way of getting the juice to ferment more quickly and reducing the risk of microbial spoilage. However, analysis of winemaking records indicated that cold settling was still being used instead of flotation in a significant number of cases. This led to a reminder being issued to the site winemakers to use flotation when possible.
The audit also evaluated and recommended natural space cooling, to bring cold air from outside into the cellar at night; insulating the remaining few uninsulated winery tanks; and trialling ultraviolet tank sanitisation technology.
Solar and storage
The winery had previously installed a 100 kW solar system and was pleased with the results but was interested in evaluating the installation of another system. This installation would be more challenging because all the roof space was already occupied, so it would have to be a groundmounted system. The new system would also put the total solar capacity over 100 kW, meaning that the new solar array would need to be classified as a power station. This changes the way energy credits are handled under the Australian Government’s Renewable Energy Target (RET) scheme. Systems under 100 kW generate small-scale technology certificates (STCs) which essentially subsidise the purchase price of the system, whereas power plants generate large-scale generation certificates (LGCs) which are awarded as generation occurs and can then be sold to generate income. The nature of the LGC market adds a layer of risk to the ongoing economics of the system.
A range of solar expansion scenarios were considered, ranging from 30 kW to 150 kW, with quotes being sourced from several suppliers. An additional 100 kW gave the lowest simple payback period. This would take the percentage of the winery’s electricity use coming from solar from 24% to 36% but would drop the overall solar utilisation from 76% to 52% (i.e. 48% exported to the grid). This is a very high level of export, but the winery faced a high peak tariff, and had negotiated a competitive buy-back rate for their exported solar-generated power, so the simple payback period was only 4.8 years. A sensitivity analysis was performed on some of the key risk factors. A worst-case scenario was constructed where the solar buyback rate was halved at the end of the current contract, and the LGC market price went to zero. In this case, the simple payback period increased to 7.6 years.
The considerable percentage of solar exported to the grid would make the site a potential candidate for battery storage, so this was also investigated. A simulation was performed based on the winery’s electricity use data to try and model the flow in and out of a battery, but the payback on a 120 kWh battery would have been approximately 13 years, making it uneconomic. There were two main contributing factors to this. Firstly, the winery’s solar buy-back rate was quite reasonable so the benefit of storing electricity over exporting it was minimal. Secondly, the winery did not have a peak demand charge component of its electricity bill, so peak shaving was of no benefit. Other scenarios such as charging batteries on much cheaper off-peak electricity and using that electricity at peak times when demand was not met by solar energy were also considered, but battery purchase was still found to be uneconomic. However, the cost of batteries is on a downward trend, so there may be a time when batteries would be a worthwhile investment for this winery. For now, they are probably more suited to wineries that face low solar buy-back rates or operate on the electricity spot market.
Conclusion
The winery involved in this case study had been very proactive in reducing its electricity use over the last 10 years. However, the new energy audit still identified several improvement opportunities with payback periods of less than five years. If these were all adopted, the winery’s ongoing electricity use would be reduced by a further 15%, not counting the proposed new solar array. While an energy audit might seem like just another thing to worry about, it can offer real insights into a winery or vineyard’s processes and the improvement opportunities it identifies can make it well worth the effort.
References and further reading
Agriculture Victoria. 2018. Agriculture Energy Investment Plan: http://agriculture.vic.gov.au/agriculture/farmmanagement/agriculture-energy-investment-plan, viewed 19/6/2018.
The Australian Wine Research Institute (AWRI). 2012. Refrigeration: https://www.awri.com.au/commercial_services/ environmental-strategy/refrigeration/, viewed 21/6/2018.
The Australian Wine Research Institute (AWRI). 2018. Grants: https://www.awri.com.au/information_services/ grants/, viewed 25/6/2018.
Sustainability Victoria. 2018. Energy Assessment Grants: http://www.sustainability.vic.gov.au/About-Us/Grants-andFunding/Energy-assessment-grants, viewed 19/6/2018.
US Department of Energy. 2004. Minimising Compressed Air Leaks – Compressed Air Tip Sheet #3: https://www1.eere.energy.gov/manufacturing/tech_assistance/pdfs/compressed_air3.pdf, viewed 20/6/2018.
Note This case study by Tadro Abbott was first published in AWRI Technical Review No. 235 in August 2018.